The significance of water volume measurement is growing, particularly in large diameters. The challenge related to fresh water or cooling water processes is to form accurate flow recordings or to document and control individual consumptions and withdrawal volumes. However, flow detection particularly in large diameters is very challenging. In such situations, the transit time measurement – because of its high flexibility as a reliable and cost-efficient measurement system – is literally created for permanent flow metering.
Figure 1.
Securing the Water Supply
The requirement for a number of processes is to consume as little fresh water as possible. Water feed and withdrawal quantities also have to be monitored continuously. All these tasks mean that the flow rates have to be permanently examined and verified. Integration into higher systems such as SCADA systems is vital as the systems are usually used within large areas.
Conception and Selecting the Measurement System
为了保证恒定的流记录,measurement systemthat can establish the medium velocity covering the whole wetted area has to be used. This is particularly vital with varying flow conditions. Most of the measurement systems that are usually used either provide only the spot velocity measurement or the required penetration depth. Quite basically, when it comes to installation, certain measurement systems either entail too many costs or require too many employees. Measuring high medium velocities to many systems is also an equally difficult task.
One cost-efficient method to obtain reliable information on the prevailing flow/discharge is the measurement using the ultrasonic transit time difference principle. Such types of systems are prominent for low maintenance expenses and high operational safety. They can be flexibly used with all the required sizes and media. When compared to other techniques, the measurement system also has the benefit to be largely autonomous of the media’s properties to measure such as fluctuating temperatures, viscosity, or electrical conductivity.
该测量原理基于直接定义两个超声传感器之间声信号的传输时间。这种类型的传感器也被描述为水声转化器(下面提供的图中的A和B)。两种声音冲动彼此依次依次发送,然后测量发射器和接收器之间的不同运输时间。下游行驶(T2)的冲动比上游的冲动(T1)更快地到达接收器。
Extremely accurate time measurements and a signal correlation were used to measure the mandatory times. This signal correlation compares the signal transmitted with the signal received by the opposite converter. Thus, the comparison enables the determination of the accurate moments of transmission and reception of the measurement signal. The difference between both determined times is proportional to the average flow velocity within the measurement path.
.jpg)
Figure 2.Schematic illustration of transit time difference principle.
t1 = Impulse time against flow direction
t2 = Impulse time in flow direction
L = Transit time / distance between sensors
公式:Average transit time difference in a measurement path
The average cross-sectional velocity can be established by using this formula, and thus the flow rate from the measured average velocities within the different layers is related to the velocity coefficients accordingly.
Q = flow rate
k = measurement place-specific correction factor
A = wetted area
VG =平均速度
公式:General flow calculation
The more measurement paths are used, the more data on the flow profile predominant at the measurement spot can be acquired. Here, the total flow rate is the total of the individual flow rates. Thus, the accuracy of the flow rate determination will be increased using numerous measurement paths. The effects of disturbing flows crossing the main flow direction can be decreased by arranging the sensors of a multi-path measurement crosswise. Cross flows may result in measurement errors. If a multi-path measurement arrangement is used, it may also decrease the length of intake and discharge sections required to calm down the flow profile at the measurement point.
.jpg)
Figure 3.Schematic illustration of multiple measurement paths.
由于新的计算流体动力学(CFD)模型和在领先机构的深入测试,因此可以检查常规干扰下游的流动剖面的行为和效果。根据结果,可以将流量曲线直接合并为肘部的下游,并将其他干扰直接在测量系统发射机中的计算模型中组合在一起。仅需要指示与测量点的距离和干扰类型。从这些规格中,测量可以自动确定要使用的校正因子。因此,流量测量的结果非常准确,也可以与较短的镇静和进气门一起使用。
.jpg)
图4。CFD模型的干扰(elbow).
Nivus GmbH的新设备类型允许运输时间技术既可以用作夹具系统和侵入性测量。在这里,必须根据测量位置的情况选择所使用的传感器类型。在定义的布置中,使用具有湿传感器的多路径系统可以帮助实现最大测量精度。如果传感器不能插入过程(磨料,腐蚀性或其他有问题的介质),则可以从外侧安装在管道上而不会干扰过程(夹紧测量系统)。
Implementing a Measurement
.jpg)
.jpg)
.jpg)
图5。Transmitter and various sensor types.
Tasks of the example shown: long-term recording of flow velocity and flow rate for archiving in a drinking water supply pipeline of a distribution system operator.
Here, accuracy needs are very high as the measurement place has to be used for billing purposes.
ANivuflow 600系统with invasive sensors by NIVUS GmbH was used. By using tapping nozzles, the sensors were inserted into the pipe. This is how the readings can be provided to the following SCADA system with the preferred level of accuracy through data connection. The broad range of sensors and installation material enables picking up readings at various measurement spots.
A very minimalistic technique can be followed in terms of spare parts stock:
There is no need to stock diameter-specific parts; there is one measurement system for almost all pipe diameters and measurement places.
概括
基于超声传输时间方差原理,流量测量have undergone a number of years of elaborate testing. They have also been demonstrated to be effective in practical use and stand out for a high level of flexibility and accuracy with regards to applicability in different measurement places. Owing to ease of maintenance and robustness, the ultrasonic transit time principle is suitable for measuring in pipes with smaller diameters (such as cooling water or process water) and also for permanent measurements on challenging measurement sites (such as hydro-electric plants, high process water volumes, large pipe diameters, and varying media).
However, with new-generation devices, the technique’s benefits have been significantly extended. Among other things, accuracies of flow measurements and measurement ranges have been considerably increased.
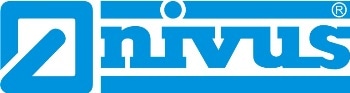
此信息已从Nivus GmbH提供的材料中采购,审查和调整。欧洲杯足球竞彩
For more information on this source, please visitNIVUS GmbH。