施耐德博士的CAE工程师Przemyslaw Narowski解释了注射的真实需求-他公司内部出现了模拟模拟过程,以及选择Modex3D的原因。
moldex3d.用于新设计零件的可行性分析,Moldex3D其他仿真解决方案的增加应用扩大了他们的技术能力和未来的前景,从CAD到CAE到CAM的流线型工程工作流。他的故事展示了多个真实场景,以说明Moldex3D结果和值的准确性。
挑战
- 由于空气疏水阀引起的表面缺陷
- 严重的产品翘曲
- 找到有效的排气腔
解决方案
Modex3D可用于将燃料填料部分中的翘曲量减少40%以保证尺寸精度。通过使用Moldex3D,也可以消除汽车内部部件表面上的空气陷阱。
好处
- 调查新设计的可行性,例如,估计的周期时间和理想的浇口位置
- 克服坚韧的成型挑战,如翘曲(40%)和空气陷阱
- 鼓励“反向仿真”对未来产品开发方向的概念
案例研究
主要目的是验证准确性Moldex3D模拟结果与实际实验情况进行了对比,进一步防止了产品的高翘曲和明显的气阱问题。
在第一种情况下,施耐德博士利用Moldex3D模拟了导向元件(图1)和汽车电话亭杆(图2)的翘曲行为,仿真结果与实验结果吻合。
图1。引导元件的模拟与现实的翘曲结果。
*模拟和真实翘曲的匹配近乎完美
.jpg)
图2。翘曲分析结果与实际测量结果比较。
在第二种情况下,使用Moldex3D预测加油杆及其盖的过度翘曲和空气陷阱。这些潜在的困难可能导致装配失败,并对零件的外观产生影响。
施耐德博士使用Moldex3D开发了一种创新设计,将最大收缩率区域的材料数量减少了一半(图3),并确定了适当的排气位置(图4)。因此,预测表明,总翘曲位移有了相当大的改善。
.jpg)
图3。优化设计使最大收缩区域的材料用量减少了一半。
.jpg)
图4。Moldex3D可以精确预测空气陷阱的位置,并确定合适的排气位置。
施耐德博士使用Moldex3D模拟了原始设计和改进后的设计。对原始设计的分析结果表明,高收缩会发生在零件的厚区域(图5),并导致过度翘曲。在改变零件厚度后,预测显示翘曲位移减少了近40%(图6)。
.jpg)
图5。在原始设计中预测了过度的翘曲。
.jpg)
图6。总翘曲位移减少了近40%。
结果
在...的帮助下moldex3d分析,施奈德博士对翘曲和填补行为进行了清晰的见解,可以预测实际生产前的潜在缺陷。目前,在Schneider博士,Moldex3D是在产品开发阶段的可行性研究中最重要的工具之一。每个注塑设计是必要的,以进行模具填充分析。例如,如果有一些不适的东西,如果翘曲值是不可取的,施奈德博士的团队将采取纠正措施。总之,施耐德博士能够成功地克服制造问题,优化产品和模具设计,这有助于在实际生产之前有效地降低模具改性成本和模具试验。
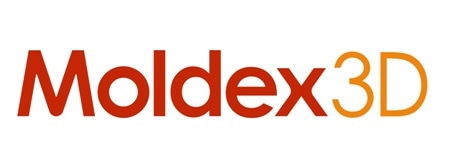
此信息已采购,审查和调整由Moldex3D提供的材料。欧洲杯足球竞彩
有关此来源的更多信息,请访问Moldex3D。